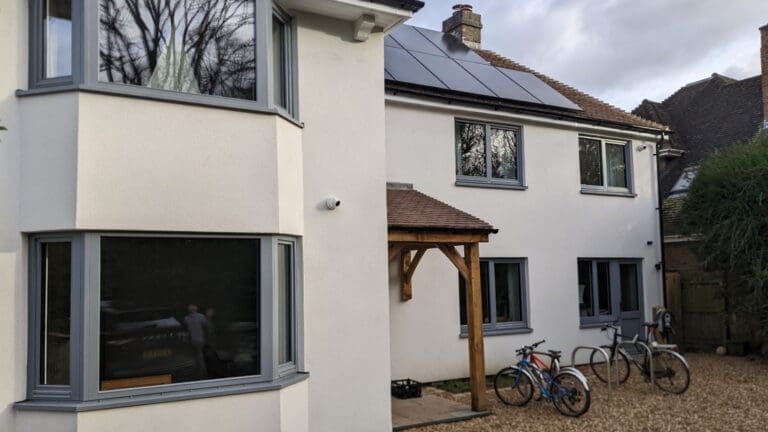
An engineer by profession, Stuart’s career followed a different direction to his self-professed energy geek passions which, for a long time, were consigned to ‘hobby’ status.
Stuart’s fascination with energy blossomed alongside a career which included ‘lots of 3D printing, material selection and other fun things’.
Until, that is, a few years ago, when Stuart stumbled across the vibrant Cambridge retrofit scene. With great groups set up to support those making the move to low carbon living, Stuart found plenty to feed his growing geek habit. Eco home tours of retrofitted and passive houses, and lectures organised in hired halls to bring together householders and installers, fed a hunger for the possibilities of retrofit.
With a head full of accumulated understanding, Stuart’s own retrofit journey began around five or six years ago with a purchase of a 1930s property and designs on changing it ‘a reasonable amount’.
Following this journey, the inevitable happened. Toward the end of 2023, Stuart left behind the world of machine learning for a more sustainable path as he joined Midsummer Energy making his passion for all things sustainable his profession.
“In my previous career we did some great things in developing new materials, but the joy went out of it as some of it was too oil company based. I went with my instincts and moved to something that’s a lot more sustainable.
“I guess that makes me a climate quitter!”
Passive House standard
Stuart takes up the retrofit story: “I put some plans together. My architect surveyed the house and drew up plans in 2018, and found the right builder to help make them a reality. The work itself has taken around a year and a bit to do.
“As an engineer myself, it was great to be involved from the start and my aim was to improve the energy efficiency as much as possible and deliver maximum air tightness.
We wanted to go for Passive House EnerPHit standard, with the AECB Standard as a fall back, so our architect built a PHPP base model and then was able to model different added insulation thicknesses and materials. This was useful later as we could also try out materials with lower embodied carbon, using PH Ribbon.
“It took three or four years from initial design, through me changing and evolving the ideas. We then approached five different builders.
“Three talked to us and, of the three, one never followed up – two did, but one pulled out just before the price was to be submitted – so it is tricky finding the right builder for retrofit.
“We started with outside work in June 2022, moved out into a house nearby, around August/ September when the work broke through into the house, then moved back in in May 2023.”
The project
“One key advantage we had was room for external wall insulation, with quite an overhang under the eaves, so we were able to fit 150 millimetres of external wall insulation.
“We ended up with two different types. The first was PIR – Kingspan Kooltherm – with a better U value, which can leave the joints visible, so the builder prefers to add a layer of EPS, which is very easy to work with.
“We debated replacing the suspended timber floors with highly insulated concrete and underfloor heating, but in the end decided to rip all the floors up to insulate underneath. We triple glazed the whole house and added an air source heat pump.
“Interestingly, as soon as you reduce energy loss and the energy use for heat, you become far more aware of the energy used for hot water, so we added a Showersave wastewater heat recovery system too.
“The heat pump we fitted is a Samsung HTQ and the architect recommended adding Homely to optimise the system which we did. It basically controls the system, to run it in the most efficient way and keep flow temperatures as low as possible.
“Now, through my work with Midsummer, I’m trialling some different set ups. One is to run the heat pump on cheap night tariffs. It preheats the house on the 7.5p per kWh tariff to take it above our desired comfort temperature. One of Homely’s features is that it learns how the house heats and cools down, so it knows what temperature it needs to reach on the cheap tariff to achieve our desired 20 degrees for the evening.
“The other experiment we’re doing is developing the system to take PV production into account.
“We have twenty-one 405W solar panels on the roof. I fitted an Eddi solar power diverter, but since Octopus changed their pricing, it makes more sense to export excess generation and get paid 15p per unit than it does to divert it to the DHW. We also have an EV, so the Zappi Charger can also soak up excess.
“One of our key objectives was to achieve the best possible airtightness so we also installed a Zehnder MVHR system which delivered an unexpected benefit. I’m not a great fan of built-in wardrobes, but my wife is, and she was delighted when they turned out to be a great way to hide the MVHR ducts!”
So, did you achieve the ultimate eco house?
“Well, we certainly got close.
We haven’t quite achieved the airtightness we were hoping to. Below 3 is what we needed for the MVHR and we are at 2.11, which is excellent, but as the build progressed we couldn’t fit the roof we’d planned on which had a knock on effect.
“The resulting delay meant that we couldn’t do the airtightness testing we planned to do at first, second fix etc. As a result, we didn’t get as airtight as we would have liked.
“As I’ve mentioned, Cambridge is a fantastic place to live for support with retrofit. A neighbour built himself a ground source heat pump, as you do, and also built a fan that fits in the window and locates leaks for the builders to fill in as you go along. That helped us to achieve such a good result.
“The domestic hot water went into the loft along with the MVHR, so we moved all the insulation from floor level to roof level taking out the poor existing ceiling insulation that was there and using it between the floorboards – great for acoustic properties and better than throwing it away.
“We used around 200mm of glass fibre and PIR insulation in between and under the rafters, and then OSB boards under that. We covered it with airtightness tape and paint and taped quite a lot of the joints. We also used a lot of Passive Purple (an airtight, liquid, vapour-controlled membrane) in the roof, and still had to go around a number of times to find the holes. All the roof members move with wind pressure, opening up joints that have had AT paint.
“The airtightness barrier was designed to run in the roof (on the warm side of the roof insulation); there is no insulation or AT barrier in the bedroom ceilings. But we also have an airtight loft hatch – belt and braces. With the loft hatch closed, the air tightness improves to 1.77, if you include the Loft space in the volume.
“Achieving this has been hard work. Airtightness is clearly one of the biggest challenges in retrofit. In a perfect world we’d be almost perfectly airtight, a passive house, but it was hard to get down to that level.”
How about storage?
“I didn’t fit a battery, partly due to space and partly because we switched our dying diesel for an EV which effectively gives me a 60kWh battery sat on the drive – although bi-directional charging isn’t yet readily available. “With battery technology moving so quickly I decided to wait on that one.”
It’s a fast-moving sector, did anything change during the process?
“With my background in materials, I was keen to use as many eco materials as possible. In practice it wasn’t always feasible due to cost, practicality or difficulty of acquisition. Interestingly, things like lead replacement materials are well advertised, but it can be a struggle to acquire them.
“When we dug up the garage floor to insulate underneath it, we looked at foamed glass insulation, but the cost quoted was a ridiculous £14k compared to a couple of hundred pounds for PIR.
“Similarly, I would have really liked to have used fibre insulation for the external wall insulation but, with 150 millimetres, I couldn’t quite achieve the desired U-values. We did use glass fibre insulation between the roof rafters, and timber fibre insulation under the suspended timber floors – I had to argue that one with the architect!
“With ongoing work going into creating a circular economy so that expanded polystyrene and waste plastics can be reused/upcycled I am hopeful that, by the time someone’s pulling the house apart, reuse may be possible.”
What about summer?
“We’ve done a couple of things to allow for the heat of summer which may well be unnecessary. The Fakro rooflights have got see-through external blinds that cut out 85% of in-coming solar radiation, but, in any case, passive house guidance suggests keeping external windows below 20% of floor area.
“We can also run the air source heat pump backwards to cool the house and the underfloor heating, but we haven’t needed that yet.
“What frustrates me slightly about overheating is that there are some very simple changes we could make to modern homes, at almost next to no cost, to stop them overheating, but we still design houses like greenhouses which is basically a failure of building design.
“If you bring the eves out slightly further, as we did, for example, with our Sun Room, then when the sun’s high the sunlight doesn’t get into the house, avoiding overheating.”
How does it feel to live there?
“Our house varies so little in terms of temperature. It’s great. It’s amazing how clean and fresh the air is. The one thing I find strange is the silence of the heat pump.”
Data gathering
“Now the retrofit is completed, we can help guide others. There is a lot of research going on in Cambridge and I’ve signed up with Parity Projects, who are building a model to provide performance guarantees for insulation and other energy efficiency improvements.
“They’ve fitted flow sensors to measure all of the domestic hot water and the heating.
“They also fitted CT clamps to the heat pump, six temperature sensors around the house and a weather station at the bottom of the garden to develop a greater understanding and enable better modelling.
“I am also hoping we can be a case study for the Cambridge Open Eco Homes https://cambridgecarbonfootprint.org/open-eco-homes-case-studies/, so we can spread the word.
“I am often asked about the financial perspective but, for me, it is more about comfort than it is about financial return.
“Even so, there will be quite a lot of savings and we’ve got rid of our gas supply, which I’m delighted about as I dislike fossil fuels intensely.”
Did costs work out as you’d expected?
“We were slightly over-budget, but that was more down to me deciding to add extra elements along the way. My perspective was, if you’re going to invest in something, then why not invest in your house?
“People decorate their houses, or fit new kitchens, because they want to live in a nice house with no expectation of a return on investment.
“That’s my motivation – a lifestyle choice with no frustration about wasted energy – we hope to live here for at least the next 20-30 years.
You clearly have a huge passion for the project
“A lot of deep retrofits are done by engineers or geeky people who enjoy the project. I’d often find the builder and enjoy getting into the nitty gritty, working out all the options and deciding between us, with some good input from the architect, on a more cost-effective approach or one that performs better.”
But with this type of experience relatively limited, was it a challenge to find someone with that knowledge, understanding and enthusiasm?
“I think that was the trickiest thing – finding a builder with experience of such things as airtightness. For new builds, there are those who are experienced in passive house design but it’s not easy to create a passive house through retrofit.
“When you’re renovating an existing house, sometimes you don’t know what you’re dealing with until you’ve got a hole in the ground, or you’ve lifted the floorboards.”
Hindsight is a wonderful thing, but is there anything that you would do differently when you look back?
“That’s a good question and you always learn from these projects.
“The main things were the airtightness and the roof of the Sun Room extension which was probably my biggest learn in the experience.
“The new roof system that we wanted is on display in the National Retrofit Centre and looked a great solution. I just assumed it would be straightforward to source which was a bit naïve.
“It was also hard to get agreement on the design details and that could have created warranty issues so, very late in construction, we swapped from the planned steel roof to a membrane which then rendered some of the roof design details unnecessary.
“The delay disrupted the airtightness process so, in hindsight, I should have considered a few more options for the roof.
“Final decisions on the MVHR pipe runs also came through quite late, which meant that, in certain places, we have boxing that could have been avoided by using web joists to run the ducts through.
“I’ll get it right next time,”Stuart says with a smile in his voice.
“There’s always more but the question is, how far do you go? At some point you have to just get it done. My family only have so much patience…”
What about schemes or grants?
“The Boiler Upgrade Scheme was certainly welcome for the heat pump, and it was the heat pump that first led to my path crossing with Midsummer which amuses me looking back because as I say, I’ve only started working with them in the last couple of months.
“As an engineer who loves getting into the details, I was checking the sizing of the heat pump and radiators and came across their Heatpunk software, which is free, and I could put my plans into that, fairly easily work out the heat loss of the property and say, hang on, these guys are telling me I need the 14kW heat pump, but I know I can quite happily have an 8kW one.
“Even when I was just looking around the Internet for details on heat pumps, I’d end up at Midsummer’s website. So, it seems it I was destined to end up working with them!
You clearly have a huge amount of knowledge yourself from your own background but what about your average consumer – where do they find information?
“I guess I do have an advantage as an engineer so I could double check things with Midsummer’s software for example.
“But that doesn’t mean that other people can do that. There are a lot of resources available, but you might need a level of technical understanding to get into the details. In the perfect world we could turn to any builder, and they would know all this stuff but, unfortunately, it’s not like that yet.
“There is still a lot of work to do – it is an industry wide issue and, having gone through the experience, it is great to see that Midsummer is part of the solution.
“We regularly have installers come on site for training by those whose products we sell. The knowledge is out there, and we need to get it into the hands of the installers so they can support the homeowner.
“At Midsummer we make sure we have a very knowledgeable team so they can explain all the technical details and help advise on product selection.”
What is your role at Midsummer?
“I’m head of the sustainable heating team. Midsummer has predominantly been solar but, over the last three years, we have seen substantial growth in interest on the heating side and more PV installers moving into renewable heat.
“As a result, Midsummer is growing very rapidly, and I am here to assist with this growth on the heating side.”
What will be the tipping point to accelerate the uptake of renewables?
“It will take a while but, as heat pump COPs steadily rise with a better installer base, people will realise the myths are just that. As people realise that properly specified heat pumps systems are cheaper to run, then gas will naturally fall away.”
You talk with enthusiasm about your desire to live in a comfortable home yet the drive for renewables has been more about doing the right thing, have we lost the message that it is a life improvement?
“Totally. If you look at any technology update, you’ve got the early adopters who do it because they’re interested. Then you have those who feel it is a good thing to do. Then the laggards who don’t want to change anything.
“I believe we’re starting to transition from the geeks to those who will do it because it’s the right thing to do from both a cost and environmental basis but moving to that mass adoption will still need government help.
“For me personally – it has been the best decision I could have taken.”
